
Maintenance
4 Ways to Leverage Predictive Maintenance Data Analytics in Your Venue Maintenance Strategy
May 3, 2023
3 min read
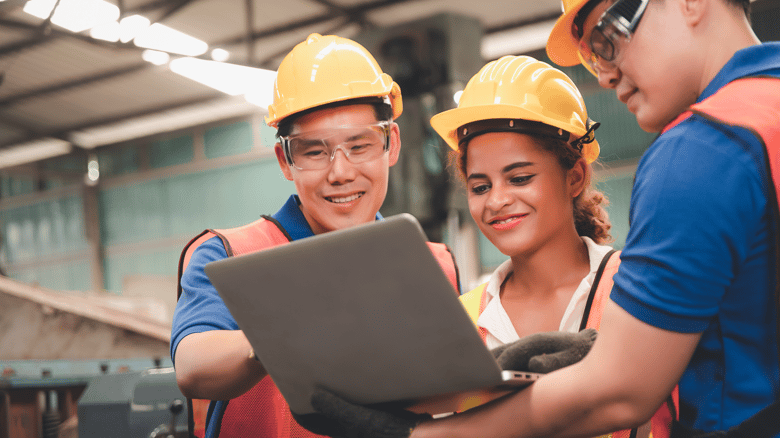
Maintenance
7 Steps Professional Facility Managers Follow to Cut Stress with a CMMS
January 25, 2022
3 min read
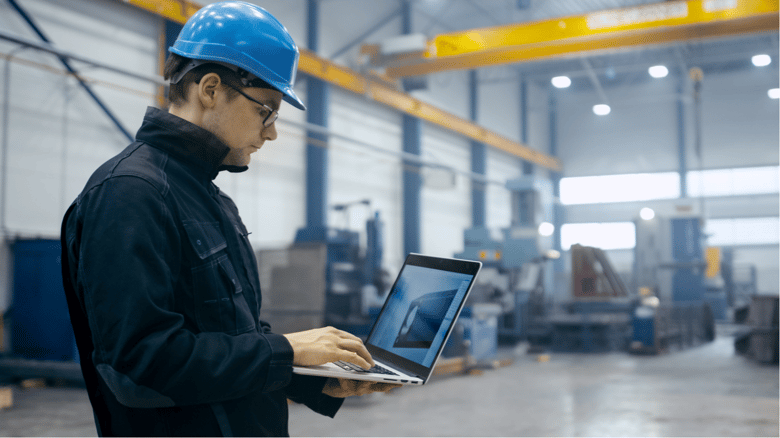
Maintenance
How to Successfully Evaluate, Implement and Optimize CMMS Software
January 11, 2022
3 min read